विविध उद्योगांमध्ये ग्राइंडिंग डिस्क्स महत्त्वाची भूमिका बजावतात, ज्यामुळे साहित्याला आकार देणे आणि फिनिशिंग करणे सोपे होते. तथापि, इतर कोणत्याही साधनांप्रमाणे, ते त्यांच्या कार्यक्षमता आणि कार्यक्षमतेला बाधा आणणाऱ्या समस्यांपासून मुक्त नाहीत. या लेखात, आपण सामान्य ग्राइंडिंग डिस्क समस्यांचा शोध घेऊ, त्यांची मूळ कारणे शोधू आणि अखंड कार्यप्रवाहासाठी प्रभावी उपाय देऊ.
परिचय
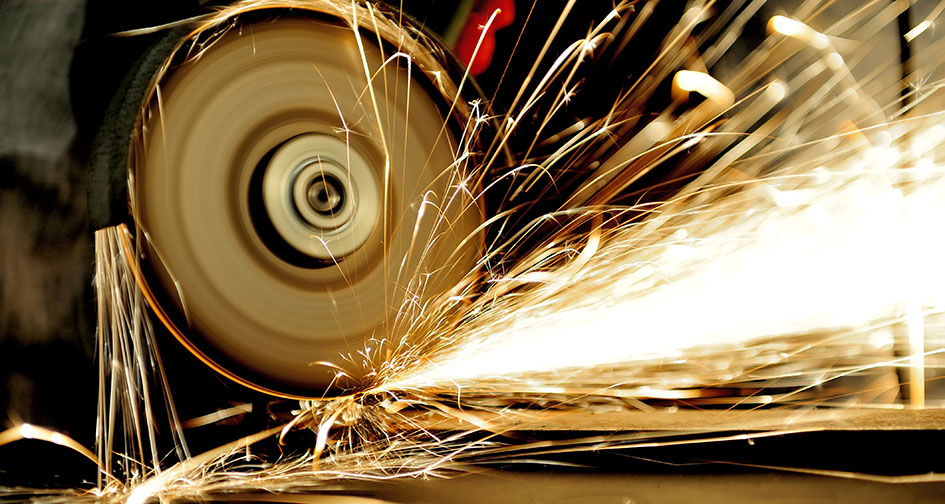
ग्राइंडिंग डिस्क विविध उद्योगांमध्ये मूलभूत भूमिका बजावतात, ते मटेरियल काढून टाकण्यासाठी, आकार देण्यासाठी आणि फिनिशिंग प्रक्रियेसाठी आवश्यक साधने म्हणून काम करतात. त्यांचा वापर अनुकूलित करण्यासाठी आणि कार्यक्षम ऑपरेशन्स सुनिश्चित करण्यासाठी त्यांची व्याख्या, उद्योगांमधील महत्त्व आणि सामान्य समस्या समजून घेणे अत्यंत महत्त्वाचे आहे.
अ. ग्राइंडिंग डिस्कची व्याख्या
ग्राइंडिंग डिस्क्स ही मशिनिंग प्रक्रियेत वापरल्या जाणाऱ्या अपघर्षक साधनांपैकी एक आहेत जी सामग्रीच्या पृष्ठभागांना कापण्यासाठी, पीसण्यासाठी किंवा पॉलिश करण्यासाठी वापरली जातात. या डिस्क्समध्ये सामान्यत: बॅकिंग मटेरियलशी जोडलेले अपघर्षक कण असतात, ज्यामुळे एक फिरणारे साधन तयार होते जे अतिरिक्त सामग्री काढून टाकू शकते, पृष्ठभाग गुळगुळीत करू शकते किंवा कडा धारदार करू शकते. ते विविध आकार आणि आकारांमध्ये येतात, प्रत्येक विशिष्ट अनुप्रयोगांसाठी डिझाइन केलेले.
ब. विविध उद्योगांमध्ये महत्त्व
धातूकाम उद्योग:
धातूच्या निर्मिती आणि उत्पादनात, धातूच्या पृष्ठभागांना आकार देण्यासाठी, डिबरिंग करण्यासाठी आणि पूर्ण करण्यासाठी ग्राइंडिंग डिस्क्स अत्यंत महत्त्वाच्या असतात. अचूक परिमाणे आणि पृष्ठभागाची गुणवत्ता प्राप्त करण्यासाठी ते सामान्यतः अँगल ग्राइंडरसह वापरले जातात.
बांधकाम उद्योग:
बांधकाम व्यावसायिक काँक्रीट पृष्ठभाग तयार करणे, खडबडीत कडा गुळगुळीत करणे आणि दगड आणि काँक्रीटसारख्या साहित्यातील अपूर्णता दूर करणे यासारख्या कामांसाठी ग्राइंडिंग डिस्कवर अवलंबून असतात.
ऑटोमोटिव्ह उद्योग:
ऑटोमोटिव्ह क्षेत्रात ग्राइंडिंग डिस्क्स हे टूल्स धारदार करण्यापासून ते धातूच्या घटकांना आकार देण्यापर्यंतच्या कामांसाठी आवश्यक आहेत. ते ऑटोमोटिव्ह पार्ट्सच्या अचूकतेत आणि गुणवत्तेत योगदान देतात.
लाकूडकाम उद्योग:
लाकडी पृष्ठभागांना आकार देण्यासाठी आणि गुळगुळीत करण्यासाठी लाकूडकाम करणारे ग्राइंडिंग डिस्क वापरतात. या डिस्क्स अतिरिक्त साहित्य काढून टाकण्यासाठी, आकार परिष्कृत करण्यासाठी आणि पुढील फिनिशिंगसाठी लाकूड तयार करण्यासाठी प्रभावी आहेत.
सामान्य उत्पादन:
ग्राइंडिंग डिस्क्स विविध उत्पादन प्रक्रियांमध्ये वापरल्या जातात जिथे अचूक सामग्री काढून टाकणे आवश्यक असते, ज्यामुळे उच्च-गुणवत्तेच्या घटकांच्या निर्मितीमध्ये योगदान मिळते.
क. भेडसावणाऱ्या सामान्य समस्या
डिस्क वेअर आणि घर्षण:
सतत वापरल्याने ग्राइंडिंग डिस्कची झीज आणि घर्षण होऊ शकते, ज्यामुळे त्याच्या कार्यक्षमतेवर परिणाम होतो. कार्यक्षमता राखण्यासाठी नियमित तपासणी आणि बदल आवश्यक आहेत.
जास्त गरम होणे:
दीर्घकाळ वापरताना जास्त घर्षणामुळे जास्त गरम होऊ शकते, ज्यामुळे डिस्कची टिकाऊपणा आणि तयार पृष्ठभागाची गुणवत्ता प्रभावित होते. योग्य थंड करण्याचे उपाय आणि वेळोवेळी ब्रेक घेणे आवश्यक आहे.
अडकणे:
डिस्क्स ग्राइंडिंग केल्याने मटेरियलचे अवशेष जमा होऊ शकतात, ज्यामुळे त्यांची प्रभावीता कमी होते. नियमित साफसफाई किंवा अँटी-क्लोजिंग वैशिष्ट्यांसह डिस्क्स निवडल्याने ही समस्या टाळण्यास मदत होते.
कंपन आणि कंपन:
असंतुलन किंवा असमान झीज यामुळे कंपन किंवा डळमळीतपणा येऊ शकतो, ज्यामुळे फिनिशची गुणवत्ता आणि ऑपरेशनची सुरक्षितता दोन्ही प्रभावित होतात. योग्य स्थापना आणि संतुलन अत्यंत महत्त्वाचे आहे.
चुकीची डिस्क निवड:
विशिष्ट मटेरियल किंवा वापरासाठी चुकीच्या प्रकारची ग्राइंडिंग डिस्क निवडल्याने अकार्यक्षमता आणि संभाव्य नुकसान होऊ शकते. मटेरियलच्या सुसंगततेवर आधारित योग्य निवड करणे आवश्यक आहे.
या साधनांवर अवलंबून असलेल्या उद्योगांसाठी ग्राइंडिंग डिस्कशी संबंधित व्याख्या, महत्त्व आणि संभाव्य आव्हाने समजून घेणे आवश्यक आहे. सामान्य समस्या सोडवून आणि योग्य वापर सुनिश्चित करून, उद्योग त्यांच्या संबंधित अनुप्रयोगांमध्ये ग्राइंडिंग डिस्कची प्रभावीता वाढवू शकतात.
ग्राइंडिंग डिस्क्सवर झीज आणि फाडणे
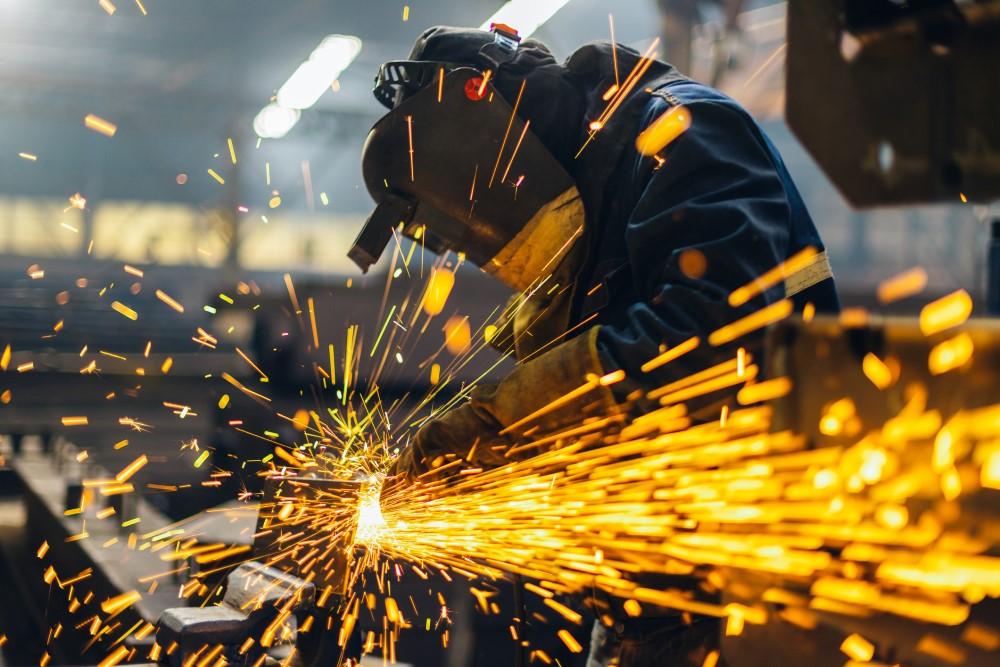
ग्राइंडिंग डिस्क्स ही विविध उद्योगांमध्ये आवश्यक साधने आहेत, जी धातूच्या निर्मितीपासून ते काँक्रीट पॉलिशिंगपर्यंतच्या कामांसाठी आवश्यक घर्षण प्रदान करतात. ग्राइंडिंग डिस्क्सची कार्यक्षमता वाढविण्यासाठी आणि सुरक्षितता सुनिश्चित करण्यासाठी त्यांच्या झीज होण्यास कारणीभूत घटक समजून घेणे अत्यंत महत्त्वाचे आहे.
साहित्याची कडकपणा आणि रचना:
कडकपणामध्ये फरक:ग्राइंडिंग डिस्क्सना वेगवेगळ्या कडकपणाच्या पातळी असलेल्या पदार्थांचा सामना करावा लागतो. धातू आणि काँक्रीट सारख्या अपघर्षक पदार्थांच्या कडकपणामध्ये लक्षणीय फरक असू शकतो. कठीण पदार्थांविरुद्ध सतत ग्राइंडिंग केल्याने झीज वाढते.
साहित्य रचना:ग्राउंडिंग केलेल्या मटेरियलमध्ये अपघर्षक घटकांची उपस्थिती ग्राइंडिंग डिस्कच्या झीजवर परिणाम करू शकते. अपघर्षक कण डिस्कच्या झीजला गती देऊ शकतात.
ग्राइंडिंग प्रेशर आणि फोर्स:
जास्त दाब:ग्राइंडिंग डिस्कवर जास्त दाब दिल्याने लवकर झीज होऊ शकते. डिस्कवर अनावश्यक ताण टाळण्यासाठी विशिष्ट वापरासाठी शिफारस केलेले दाब वापरणे आवश्यक आहे.
अपुरी शक्ती: दुसरीकडे, अपुर्या बलामुळे दीर्घकाळ पीसणे होऊ शकते, ज्यामुळे अतिरिक्त घर्षण आणि उष्णता निर्माण होऊ शकते, ज्यामुळे झीज होऊ शकते.
डिस्कची गुणवत्ता आणि रचना:
अपघर्षक साहित्याची गुणवत्ता:ग्राइंडिंग डिस्कमध्ये वापरल्या जाणाऱ्या अपघर्षक पदार्थाची गुणवत्ता त्याच्या आयुष्यमानावर लक्षणीय परिणाम करते. उच्च-गुणवत्तेचे अपघर्षक पदार्थ झीज होण्यास प्रतिकार करतात आणि तीक्ष्णता जास्त काळ टिकवून ठेवतात.
बाँडिंग एजंट:अपघर्षक कणांना एकत्र ठेवणारा बाँडिंग एजंट महत्त्वाची भूमिका बजावतो. चांगल्या प्रकारे डिझाइन केलेला बाँडिंग एजंट डिस्कची टिकाऊपणा वाढवतो.
कामाच्या वातावरणाच्या परिस्थिती:
तापमान:ग्राइंडिंग दरम्यान निर्माण होणारे वाढलेले तापमान डिस्कच्या रचनेवर परिणाम करू शकते. जास्त उष्णता बाँडिंग एजंटला कमकुवत करते आणि झीज वाढवते.
ओलावा आणि दूषित घटक:कामाच्या वातावरणात ओलावा किंवा दूषित पदार्थांच्या संपर्कात आल्याने ग्राइंडिंग डिस्कच्या अखंडतेवर परिणाम होऊ शकतो, ज्यामुळे जलद झीज होते.
ऑपरेटर तंत्र:
योग्य तंत्र:ऑपरेटर कौशल्य आणि तंत्र महत्वाचे आहे. चुकीच्या कोनात पीसणे किंवा जास्त शक्ती वापरणे यासारख्या अयोग्य वापरामुळे डिस्कची असमान झीज होऊ शकते आणि डिस्कची दीर्घायुष्य कमी होऊ शकते.
नियमित तपासणी:ऑपरेटरनी ग्राइंडिंग डिस्कचे नुकसान किंवा झीज झाल्याच्या कोणत्याही लक्षणांसाठी नियमितपणे निरीक्षण करावे. एका विशिष्ट बिंदूपेक्षा जास्त झीज झालेल्या डिस्क त्वरित बदलल्या पाहिजेत.
डिस्क आकार आणि RPM सुसंगतता:
योग्य आकारमान:ग्राइंडरसाठी योग्य डिस्क आकार वापरणे अत्यंत महत्वाचे आहे. चुकीच्या आकाराच्या डिस्क असमानपणे खराब होऊ शकतात किंवा सुरक्षिततेला धोका निर्माण करू शकतात.
RPM सुसंगतता:ग्राइंडिंग डिस्कसाठी शिफारस केलेल्या रिव्होल्यूशन प्रति मिनिट (RPM) चे पालन केल्याने इष्टतम कामगिरी सुनिश्चित होते आणि अकाली झीज होण्यास प्रतिबंध होतो.
नियमित देखभाल, शिफारस केलेल्या ऑपरेटिंग परिस्थितींचे पालन आणि कामासाठी योग्य ग्राइंडिंग डिस्क निवडणे हे झीज कमी करण्यासाठी आवश्यक पद्धती आहेत. झीज प्रभावित करणारे घटक समजून घेऊन, ऑपरेटर ग्राइंडिंग डिस्कचे दीर्घायुष्य आणि कार्यक्षमता वाढवू शकतात, ज्यामुळे सुरक्षित आणि अधिक उत्पादक ग्राइंडिंग ऑपरेशन्समध्ये योगदान मिळते.
असमान दळणे
असमान ग्राइंडिंग म्हणजे अशी परिस्थिती जिथे पृष्ठभाग ग्राइंडिंग केल्यामुळे सुसंगत आणि गुळगुळीत फिनिशिंग मिळत नाही. ही समस्या विविध कारणांमुळे उद्भवू शकते आणि वर्कपीसच्या गुणवत्तेवर परिणाम करू शकते. असमान ग्राइंडिंगला कारणीभूत असलेले सामान्य घटक आणि संभाव्य उपाय येथे आहेत:
चुकीची ग्राइंडिंग व्हील निवड:
उपाय:ग्राइंडिंग व्हील हे ग्राइंडिंग मटेरियलसाठी योग्य आहे याची खात्री करा. वेगवेगळ्या मटेरियलना विशिष्ट अपघर्षक गुणधर्मांची आवश्यकता असते. वापरण्यासाठी योग्य चाक प्रकार, ग्रिट आकार आणि बॉन्ड निवडा.
चुकीचा चाक ड्रेसिंग:
कारण:योग्यरित्या न घातलेले ग्राइंडिंग व्हील असमान झीज आणि अप्रभावी कटिंग होऊ शकते.
उपाय:ग्राइंडिंग व्हीलचा आकार राखण्यासाठी आणि जमा झालेले कोणतेही कचरा काढून टाकण्यासाठी नियमितपणे ड्रेसिंग करा. योग्य ड्रेसिंगमुळे कटिंग पृष्ठभाग सुसंगत राहतो.
अपुरा ग्राइंडिंग फ्लुइड किंवा शीतलक:
कारण:ग्राइंडिंग फ्लुइडचा अपुरा किंवा अयोग्य वापर केल्याने घर्षण आणि उष्णता वाढू शकते, ज्यामुळे ग्राइंडिंग असमान होते.
उपाय:उष्णता कमी करण्यासाठी आणि घर्षण कमी करण्यासाठी योग्य ग्राइंडिंग फ्लुइड किंवा शीतलक वापरा. एकसमान परिणाम मिळविण्यासाठी योग्य थंड करणे आवश्यक आहे.
चुकीचे ग्राइंडिंग पॅरामीटर्स:
कारण:जास्त वेग, फीड रेट किंवा कटची खोली यासारखे चुकीचे ग्राइंडिंग पॅरामीटर्स वापरल्याने ग्राइंडिंग असमान होऊ शकते.
उपाय:मटेरियल आणि अॅप्लिकेशन आवश्यकतांनुसार ग्राइंडिंग पॅरामीटर्स समायोजित करा. इष्टतम सेटिंग्जसाठी उत्पादकाच्या शिफारशी पहा.
जीर्ण झालेले ग्राइंडिंग व्हील:
कारण:जीर्ण झालेले ग्राइंडिंग व्हील कटिंग पृष्ठभागाला सुसंगतता देऊ शकत नाही, ज्यामुळे ग्राइंडिंग असमान होते.
उपाय:ग्राइंडिंग व्हील त्याच्या वापरण्यायोग्य आयुष्याच्या शेवटी पोहोचल्यावर ते बदला. झीज झाल्याच्या लक्षणांसाठी नियमितपणे चाकाची तपासणी करा.
असमान दाब किंवा फीड रेट:
कारण:ग्राइंडिंग दरम्यान असमान दाब किंवा विसंगत फीड रेटमुळे सामग्री अनियमितपणे काढून टाकली जाऊ शकते.
उपाय:वर्कपीसवर एकसमान दाब द्या आणि एकसमान फीड रेट ठेवा. ऑपरेटर कौशल्य आणि तपशीलांकडे लक्ष देणे अत्यंत महत्त्वाचे आहे.
मशीन समस्या:
कारण:ग्राइंडिंग मशीनमधील यांत्रिक समस्या, जसे की चुकीचे संरेखन किंवा स्पिंडलमधील समस्या, यामुळे ग्राइंडिंग असमान होऊ शकते.
उपाय:ग्राइंडिंग मशीनची नियमित देखभाल तपासणी करा. योग्य कार्यक्षमता सुनिश्चित करण्यासाठी कोणत्याही यांत्रिक समस्या त्वरित सोडवा.
वर्कपीस फिक्स्चरिंग:
कारण:खराब बांधलेल्या किंवा चुकीच्या पद्धतीने जुळवलेल्या वर्कपीसमुळे असमान पीस होऊ शकते.
उपाय:वर्कपीसची योग्य फिक्स्चरिंग आणि संरेखन सुनिश्चित करा. ग्राइंडिंग प्रक्रियेदरम्यान हालचाल टाळण्यासाठी ते घट्ट बांधा.
असमान ग्राइंडिंगचे निराकरण करण्यासाठी योग्य उपकरणे सेटअप, योग्य ऑपरेटिंग पॅरामीटर्स आणि नियमित देखभाल पद्धतींचे संयोजन आवश्यक आहे. ग्राइंडिंग अनुप्रयोगांमध्ये उच्च-गुणवत्तेचे आणि सातत्यपूर्ण परिणाम मिळविण्यासाठी ऑपरेटरना समस्या त्वरित ओळखण्यासाठी आणि त्या दुरुस्त करण्यासाठी प्रशिक्षित केले पाहिजे. नियमित तपासणी आणि सर्वोत्तम पद्धतींचे पालन केल्याने ग्राइंडिंग प्रक्रियेदरम्यान कार्यक्षम आणि एकसमान सामग्री काढून टाकण्यास हातभार लागतो.
जास्त गरम होण्याच्या समस्या
ग्राइंडिंग दरम्यान जास्त गरम होणे ही एक सामान्य समस्या आहे जी ग्राइंडिंग व्हील आणि वर्कपीस दोन्हीच्या कार्यक्षमतेवर परिणाम करू शकते. जास्त उष्णतेमुळे विविध समस्या उद्भवू शकतात, ज्यामध्ये चाकांचे आयुष्य कमी होणे, वर्कपीसचे थर्मल नुकसान आणि एकूणच कमी होणारी ग्राइंडिंग कार्यक्षमता यांचा समावेश आहे. अतिउष्णतेच्या समस्या सोडवण्यासाठी येथे संभाव्य कारणे आणि उपाय आहेत:
चुकीचे ग्राइंडिंग पॅरामीटर्स:
कारण:जास्त वेग, फीड रेट किंवा कटची खोली यासारखे अयोग्य ग्राइंडिंग पॅरामीटर्स वापरल्याने जास्त उष्णता निर्माण होऊ शकते.
उपाय:शिफारस केलेल्या मर्यादेत ग्राइंडिंग पॅरामीटर्स समायोजित करा. ग्राइंडिंग केलेल्या मटेरियलवर आधारित इष्टतम सेटिंग्जसाठी उत्पादकाच्या मार्गदर्शक तत्त्वांचा सल्ला घ्या.
अपुरे थंडीकरण किंवा स्नेहन:
कारण:शीतलक किंवा ग्राइंडिंग द्रवपदार्थाचा अपुरा वापर केल्याने घर्षण आणि उष्णता वाढू शकते.
उपाय:ग्राइंडिंग प्रक्रियेदरम्यान शीतलक किंवा वंगणाचा पुरेसा पुरवठा सुनिश्चित करा. योग्य थंड केल्याने उष्णता कमी होण्यास मदत होते आणि थर्मल नुकसान टाळता येते.
चुकीची चाके निवड:
कारण:ग्राइंडिंग मटेरियलसाठी अयोग्य स्पेसिफिकेशन असलेले ग्राइंडिंग व्हील निवडल्याने जास्त गरम होऊ शकते.
उपाय:विशिष्ट वापरासाठी योग्य अॅब्रेसिव्ह प्रकार, ग्रिट आकार आणि बॉन्ड असलेले ग्राइंडिंग व्हील निवडा. मटेरियलशी चाक जुळवल्याने उष्णता निर्माण कमी होते.
वर्कपीस मटेरियलच्या समस्या:
कारण:काही पदार्थ, विशेषतः ज्यांचे थर्मल चालकता कमी असते, ते पीसताना जास्त गरम होण्याची शक्यता जास्त असते.
उपाय:कमी थर्मल चालकता असलेल्या पदार्थांसाठी ग्राइंडिंग पॅरामीटर्स समायोजित करा. उष्णता-संवेदनशील पदार्थांसाठी डिझाइन केलेले विशेष ग्राइंडिंग व्हील वापरण्याचा विचार करा.
चाकांच्या ड्रेसिंगच्या समस्या:
कारण:ग्राइंडिंग व्हीलची अनियमितता किंवा अयोग्य ड्रेसिंगमुळे असमान संपर्क आणि उष्णता जमा होऊ शकते.
उपाय:ग्राइंडिंग व्हीलचा आकार राखण्यासाठी आणि ग्लेझिंग किंवा साचलेला कचरा काढून टाकण्यासाठी नियमितपणे त्याला सजवा. योग्यरित्या सजवलेल्या चाकांमुळे ग्राइंडिंगची सातत्यपूर्ण कामगिरी सुनिश्चित होते.
मशीनची अपुरी देखभाल:
कारण:खराब देखभाल केलेल्या ग्राइंडिंग मशीनमुळे जास्त गरम होण्याची समस्या उद्भवू शकते.
उपाय:ग्राइंडिंग मशीनची नियमित देखभाल करा, ज्यामध्ये शीतलक प्रणाली तपासणे, चाकांच्या ड्रेसिंग उपकरणांची तपासणी करणे आणि योग्य संरेखन सुनिश्चित करणे समाविष्ट आहे. कोणत्याही यांत्रिक समस्या त्वरित दूर करा.
अपुरा चाक शीतलक प्रवाह:
कारण:ग्राइंडिंग झोनमध्ये अपुरा शीतलक प्रवाह झाल्यामुळे उष्णता कमी होऊ शकते.
उपाय:शीतलक वितरण प्रणाली तपासा आणि ऑप्टिमाइझ करा. शीतलक कार्यक्षमता राखण्यासाठी शीतलक प्रभावीपणे ग्राइंडिंग झोनमध्ये पोहोचतो याची खात्री करा.
जास्त पीसण्याचा वेळ:
कारण:ब्रेकशिवाय दीर्घकाळ दळण्याचे सत्र उष्णता जमा होण्यास हातभार लावू शकते.
उपाय:जास्त उष्णता जमा होऊ नये म्हणून अधूनमधून ग्राइंडिंग करा आणि ब्रेक द्या. मोठ्या किंवा आव्हानात्मक ग्राइंडिंग कामांसाठी हा दृष्टिकोन विशेषतः महत्वाचा आहे.
ग्राइंडिंगमध्ये जास्त गरम होण्याच्या समस्या सोडवण्यासाठी योग्य उपकरणे सेटअप, योग्य ग्राइंडिंग पॅरामीटर्स आणि नियमित देखभाल पद्धतींचा समावेश असलेला व्यापक दृष्टिकोन आवश्यक आहे. ऑपरेटरने ग्राइंडिंग प्रक्रियेदरम्यान उष्णता निर्मितीचे निरीक्षण आणि नियंत्रण केले पाहिजे जेणेकरून इष्टतम कामगिरी, विस्तारित टूल लाइफ आणि उच्च-गुणवत्तेचे परिणाम सुनिश्चित होतील.
कंपनाच्या चिंता
ग्राइंडिंग ऑपरेशन्स दरम्यान जास्त कंपनामुळे विविध समस्या उद्भवू शकतात, ज्यामध्ये पृष्ठभागाची गुणवत्ता कमी होणे, उपकरणांचा झीज वाढणे आणि ग्राइंडिंग मशीनचे संभाव्य नुकसान यांचा समावेश आहे. अचूक आणि कार्यक्षम ग्राइंडिंग प्रक्रिया साध्य करण्यासाठी कंपन समस्यांचे निराकरण करणे अत्यंत महत्वाचे आहे. कंपन समस्या कमी करण्यासाठी येथे संभाव्य कारणे आणि उपाय आहेत:
असमान चाकांचा झीज:
कारण:ग्राइंडिंग व्हीलवरील अनियमित झीजमुळे वर्कपीसशी असमान संपर्क होऊ शकतो, ज्यामुळे कंपन होऊ शकते.
उपाय:ग्राइंडिंग व्हीलची नियमित तपासणी करा आणि पृष्ठभाग सपाट ठेवण्यासाठी त्याची रचना करा. योग्य चाक देखभालीमुळे कंपन कमी होण्यास मदत होते.
असंतुलित ग्राइंडिंग व्हील:
कारण:ग्राइंडिंग व्हीलमधील असंतुलन, मग ते असमान झीज किंवा उत्पादन दोषांमुळे असो, कंपनास कारणीभूत ठरू शकते.
उपाय:व्हील बॅलन्सर वापरून ग्राइंडिंग व्हील संतुलित करा. बॅलन्सिंगमुळे वजनाचे समान वितरण होते आणि ऑपरेशन दरम्यान कंपन कमी होते.
अपुरे मशीन कॅलिब्रेशन:
कारण:चाकाच्या स्पिंडल किंवा वर्कटेबलसारख्या मशीनच्या घटकांचे चुकीचे कॅलिब्रेशन किंवा चुकीचे संरेखन यामुळे कंपन होऊ शकतात.
उपाय:योग्य कार्यक्षमता सुनिश्चित करण्यासाठी मशीनचे घटक नियमितपणे कॅलिब्रेट करा आणि संरेखित करा. मशीन सेटअप आणि संरेखनासाठी उत्पादकाच्या मार्गदर्शक तत्त्वांचे पालन करा.
वर्कपीस असंतुलन:
कारण:असमान किंवा अयोग्यरित्या सुरक्षित केलेले वर्कपीस असंतुलन निर्माण करू शकते आणि कंपनांना कारणीभूत ठरू शकते.
उपाय:वर्कपीस योग्यरित्या सुरक्षित करा, ते समान स्थितीत आणि क्लॅम्प केलेले असल्याची खात्री करा. ग्राइंडिंग प्रक्रिया सुरू करण्यापूर्वी कोणत्याही असंतुलनाच्या समस्या सोडवा.
चुकीची चाके निवड:
कारण:अयोग्य स्पेसिफिकेशन्स असलेले ग्राइंडिंग व्हील वापरल्याने कंपन होऊ शकते.
उपाय:ग्राइंडिंग व्हील निवडा ज्यामध्ये योग्य अॅब्रेसिव्ह प्रकार, ग्रिट आकार आणि बॉन्ड असेल. अॅप्लिकेशनशी जुळणारे व्हील कंपन कमी करते.
मशीनमधील झीज आणि फाड:
कारण:बेअरिंग्ज किंवा स्पिंडल्ससारखे जीर्ण झालेले किंवा खराब झालेले मशीन घटक कंपनांना कारणीभूत ठरू शकतात.
उपाय:नियमितपणे मशीनचे जीर्ण झालेले भाग तपासा आणि बदला. योग्य देखभालीमुळे जास्त कंपन टाळण्यास मदत होते आणि ग्राइंडिंग मशीनचे आयुष्य वाढते.
अपुरा शीतलक प्रवाह:
कारण:ग्राइंडिंग झोनमध्ये अपुरा शीतलक प्रवाह झाल्यामुळे उष्णता जमा होऊ शकते आणि कंपन होऊ शकते.
उपाय:योग्य थंडावा सुनिश्चित करण्यासाठी शीतलक वितरण प्रणाली ऑप्टिमाइझ करा. प्रभावी थंडावा थर्मल विस्तार आणि आकुंचन होण्याचा धोका कमी करतो, ज्यामुळे कंपन होऊ शकतात.
टूल होल्डर समस्या:
कारण:टूल होल्डर किंवा स्पिंडल इंटरफेसमधील समस्यांमुळे कंपन होऊ शकतात.
उपाय:टूल होल्डर सुरक्षितपणे बसवलेला आहे आणि स्पिंडलशी योग्यरित्या संरेखित केलेला आहे याची खात्री करा. कंपन कमी करण्यासाठी उच्च-गुणवत्तेचे आणि योग्यरित्या देखभाल केलेले टूल होल्डर वापरा.
मशीन फाउंडेशन:
कारण:खराब यंत्राचा पाया किंवा अपुरा आधार यामुळे कंपन वाढू शकतात.
उपाय:ग्राइंडिंग मशीन स्थिर आणि योग्यरित्या डिझाइन केलेल्या पायावर बसवले आहे याची खात्री करा. मशीनमध्ये प्रसारित होणारी कंपने कमी करण्यासाठी कोणत्याही स्ट्रक्चरल समस्यांचे निराकरण करा.
ग्राइंडिंगमधील कंपन समस्या प्रभावीपणे सोडवण्यासाठी योग्य मशीन देखभाल, चाकांची निवड आणि वर्कपीस हाताळणी यांचे संयोजन आवश्यक आहे. ऑपरेटरनी समस्या ओळखण्यासाठी आणि त्वरित सोडवण्यासाठी नियमित तपासणी आणि देखभाल पद्धती अंमलात आणल्या पाहिजेत, ज्यामुळे ग्राइंडिंगची कार्यक्षमता आणि गुणवत्ता सुधारते.
ग्राइंडिंगमध्ये लोडिंग समस्या
ग्राइंडिंगमध्ये लोडिंग म्हणजे अशी घटना जिथे ग्राइंडिंग व्हीलवरील अपघर्षक धान्यांमधील जागा ग्राइंडिंग मटेरियलने भरली जाते, ज्यामुळे कटिंगची क्रिया कमी होते आणि घर्षण वाढते. लोडिंगमुळे ग्राइंडिंग प्रक्रियेची कार्यक्षमता आणि गुणवत्ता यावर नकारात्मक परिणाम होऊ शकतो. लोडिंग समस्या सोडवण्यासाठी येथे संभाव्य कारणे आणि उपाय आहेत:
मऊ वर्कपीस मटेरियल:
कारण:मऊ पदार्थ बारीक केल्याने अपघर्षक धान्ये जलद अडकू शकतात.
उपाय:मऊ पदार्थांवर काम करताना खरखरीत काजळी आणि उघड्या रचनेचे ग्राइंडिंग व्हील वापरा. हे जलद लोडिंग टाळण्यास मदत करते आणि कार्यक्षमतेने चिप काढण्यास अनुमती देते.
पदार्थांचे दूषितीकरण:
कारण:वर्कपीस मटेरियलमध्ये असलेले दूषित घटक, जसे की तेल, ग्रीस किंवा शीतलक अवशेष, लोडिंगमध्ये योगदान देऊ शकतात.
उपाय:दूषित पदार्थ काढून टाकण्यासाठी पीसण्यापूर्वी वर्कपीसची योग्य स्वच्छता करा. लोडिंग कमी करण्यासाठी योग्य कटिंग फ्लुइड्स किंवा शीतलक वापरा.
चुकीचा शीतलक वापर:
कारण:शीतलक अपुरा किंवा अयोग्य वापरल्याने अपुरे स्नेहन आणि थंडपणा येऊ शकतो, ज्यामुळे लोडिंग होऊ शकते.
उपाय:शीतलक प्रवाह आणि एकाग्रता ऑप्टिमाइझ करा. प्रक्रिया वंगण घालण्यासाठी आणि थंड करण्यासाठी शीतलक प्रभावीपणे ग्राइंडिंग झोनमध्ये पोहोचेल याची खात्री करा, ज्यामुळे लोडिंग टाळता येईल.
अपुरी चाकांची तीक्ष्णता:
कारण:कंटाळवाणे किंवा जीर्ण झालेले ग्राइंडिंग व्हील्स लोड होण्याची शक्यता जास्त असते कारण ते त्यांची कटिंग कार्यक्षमता गमावतात.
उपाय:ग्राइंडिंग व्हीलची तीक्ष्णता टिकवून ठेवण्यासाठी नियमितपणे ड्रेसिंग आणि तीक्ष्ण करा. ताजे अपघर्षक धान्य बाहेर काढण्यासाठी आणि कटिंगची क्रिया वाढवण्यासाठी व्हील ड्रेसर वापरा.
कमी चाकाचा वेग:
कारण:ग्राइंडिंग व्हील कमी वेगाने चालवल्याने चिप्स बाहेर काढण्यासाठी पुरेसे केंद्रापसारक बल उपलब्ध होऊ शकत नाही, ज्यामुळे लोडिंग होऊ शकते.
उपाय:विशिष्ट चाक आणि वर्कपीस संयोजनासाठी शिफारस केलेल्या वेगाने ग्राइंडिंग मशीन चालत असल्याची खात्री करा. जास्त गतीमुळे चिप चांगल्या प्रकारे काढण्यास मदत होऊ शकते.
जास्त दाब:
कारण:पीसताना जास्त दाब दिल्यास ते साहित्य चाकात घुसू शकते, ज्यामुळे लोडिंग होऊ शकते.
उपाय:मध्यम आणि सातत्यपूर्ण ग्राइंडिंग प्रेशर वापरा. जास्त दाब न पडता चाक कार्यक्षमतेने कापता यावे यासाठी फीड रेट समायोजित करा ज्यामुळे लोडिंग होऊ शकते.
चुकीचे चाक तपशील:
कारण:ग्राइंडिंग व्हील वापरल्याने मटेरियल ग्राउंडिंगसाठी चुकीच्या स्पेसिफिकेशनसह लोडिंग होऊ शकते.
उपाय:विशिष्ट वापरासाठी योग्य अॅब्रेसिव्ह प्रकार, ग्रिट आकार आणि बॉन्ड असलेले ग्राइंडिंग व्हील निवडा. मटेरियलशी चाक जुळवल्याने लोडिंग टाळण्यास मदत होते.
कूलंटची अपुरी स्वच्छता:
कारण:दूषित किंवा जुने शीतलक लोडिंगच्या समस्या निर्माण करू शकते.
उपाय:दूषित पदार्थ जमा होण्यापासून रोखण्यासाठी नियमितपणे कूलंट स्वच्छ करा आणि बदला. ताजे आणि स्वच्छ कूलंट स्नेहन आणि थंडपणा वाढवते, ज्यामुळे लोड होण्याची शक्यता कमी होते.
चुकीची ड्रेसिंग तंत्र:
कारण:ग्राइंडिंग व्हीलचे चुकीचे ड्रेसिंग केल्याने अनियमितता आणि लोडिंग होऊ शकते.
उपाय:योग्य ड्रेसिंग टूल वापरून चाकाला योग्यरित्या सजवा. लोडिंग टाळण्यासाठी चाकाचे प्रोफाइल सुसंगत आणि अनियमिततामुक्त असल्याची खात्री करा.
लोडिंगच्या समस्या प्रभावीपणे सोडवण्यासाठी योग्य चाक निवड, मशीन सेटअप आणि देखभाल पद्धतींचे संयोजन आवश्यक आहे. ऑपरेटरनी शिफारस केलेल्या प्रक्रियांचे पालन केले पाहिजे, योग्य ग्राइंडिंग पॅरामीटर्स वापरावेत आणि लोडिंग कमी करण्यासाठी आणि ग्राइंडिंग कामगिरी ऑप्टिमाइझ करण्यासाठी नियमित व्हील ड्रेसिंग लागू करावे.
विविध धातूकाम आणि फॅब्रिकेशन अनुप्रयोगांमध्ये इष्टतम परिणाम मिळविण्यासाठी योग्य ग्राइंडिंग डिस्क निवडणे अत्यंत महत्वाचे आहे. निवड कोणत्या सामग्रीवर काम केले जात आहे, इच्छित फिनिशिंग आणि वापरल्या जाणाऱ्या ग्राइंडरचा प्रकार यासारख्या घटकांवर अवलंबून असते.
योग्य ग्राइंडिंग डिस्क निवडणे
साहित्य सुसंगतता:
फेरस धातू (पोलाद, लोखंड):विशेषतः फेरस धातूंसाठी डिझाइन केलेल्या ग्राइंडिंग डिस्क वापरा. या डिस्कमध्ये बहुतेकदा स्टीलच्या कडकपणासाठी योग्य असे अॅब्रेसिव्ह असतात आणि ते लोड होण्याची शक्यता कमी असते.
नॉन-फेरस धातू (अॅल्युमिनियम, पितळ):धातू अडकू नयेत म्हणून मऊ धातूंसाठी योग्य असलेल्या अॅब्रेसिव्ह असलेल्या डिस्क निवडा. अॅल्युमिनियम ऑक्साईड किंवा सिलिकॉन कार्बाइड डिस्क हे सामान्य पर्याय आहेत.
अपघर्षक साहित्य:
अॅल्युमिनियम ऑक्साईड:फेरस धातूंवर सामान्य वापरासाठी पीसण्यासाठी योग्य. हे टिकाऊ आणि बहुमुखी आहे.
झिरकोनिया अॅल्युमिना:उच्च कटिंग कार्यक्षमता आणि टिकाऊपणा देते, ज्यामुळे ते फेरस आणि नॉन-फेरस धातूंवर आक्रमक ग्राइंडिंगसाठी योग्य बनते.
सिलिकॉन कार्बाइड:अलौह धातू आणि दगड पीसण्यासाठी आदर्श. ते अॅल्युमिनियम ऑक्साईडपेक्षा तीक्ष्ण आहे परंतु कमी टिकाऊ आहे.
ग्रिट आकार:
खडबडीत काजळी (२४-३६):जलद साठा काढणे आणि हेवी-ड्युटी ग्राइंडिंग.
मध्यम ग्रिट (४०-६०):साठा काढून टाकणे आणि पृष्ठभाग पूर्ण करणे यात संतुलन राखते.
बारीक काजळी (८०-१२०):पृष्ठभाग तयार करण्यासाठी आणि हलके पीसण्यासाठी योग्य, गुळगुळीत फिनिश प्रदान करते.
चाकाचा प्रकार:
प्रकार २७ (उदासीनता केंद्र):सपाट पृष्ठभाग असलेली मानक ग्राइंडिंग डिस्क, पृष्ठभाग ग्राइंडिंग आणि कडा कामासाठी आदर्श.
प्रकार २९ (शंकूच्या आकाराचे):आक्रमक साठा काढून टाकण्यासाठी आणि पृष्ठभागाचे चांगले मिश्रण करण्यासाठी कोनदार डिझाइन.
प्रकार १ (सरळ):कट-ऑफ अनुप्रयोगांसाठी वापरले जाते. अचूक कटिंगसाठी ते पातळ प्रोफाइल प्रदान करते.
अर्ज:
पीसणे:मटेरियल काढण्यासाठी आणि आकार देण्यासाठी मानक ग्राइंडिंग डिस्क.
कटिंग:धातू कापण्यासाठी कट-ऑफ व्हील्स वापरा, ज्यामुळे सरळ आणि स्वच्छ धार मिळेल.
फ्लॅप डिस्क:ग्राइंडिंग आणि फिनिशिंग एकाच वेळी एकत्र करा. पृष्ठभागांचे मिश्रण आणि गुळगुळीत करण्यासाठी योग्य.
ग्राइंडरशी सुसंगतता:
ग्राइंडिंग डिस्क वापरल्या जाणाऱ्या ग्राइंडरच्या प्रकार आणि गतीशी सुसंगत आहे याची खात्री करा. डिस्कच्या कमाल RPM (रिव्होल्यूशन्स प्रति मिनिट) साठी उत्पादकाच्या शिफारसी तपासा.
कार्याची विशिष्टता:
जड साठा काढून टाकणे:कार्यक्षमतेने मटेरियल काढण्यासाठी खडबडीत वाळू आणि टाइप २७ किंवा टाइप २९ डिस्क निवडा.
पृष्ठभाग पूर्ण करणे:गुळगुळीत फिनिशिंगसाठी फ्लॅप डिस्कसह मध्यम ते बारीक ग्रिट्स निवडा.
सुरक्षिततेचे विचार:
सुरक्षा मार्गदर्शक तत्त्वांचे पालन करा, ज्यामध्ये सुरक्षा चष्मा आणि हातमोजे यांसारखी योग्य वैयक्तिक संरक्षक उपकरणे (पीपीई) घालणे समाविष्ट आहे.
अधिक टिकाऊपणा आणि सुरक्षिततेसाठी प्रबलित डिस्क निवडा.
ब्रँड आणि गुणवत्ता:
गुणवत्ता आणि सुसंगततेसाठी ओळखल्या जाणाऱ्या प्रतिष्ठित ब्रँडमधील डिस्क निवडा. उच्च-गुणवत्तेच्या डिस्क चांगली कामगिरी आणि टिकाऊपणा देतात.
खर्चाचा विचार:
सुरुवातीच्या किमतीचा ग्राइंडिंग डिस्कच्या अपेक्षित आयुष्यमान आणि कामगिरीशी समतोल साधा. उच्च-गुणवत्तेच्या डिस्कची सुरुवातीची किंमत जास्त असू शकते परंतु कालांतराने ते चांगले मूल्य देऊ शकतात.
या घटकांचा विचार करून, ऑपरेटर त्यांच्या विशिष्ट अनुप्रयोगांसाठी योग्य ग्राइंडिंग डिस्क निवडू शकतात, ज्यामुळे कार्यक्षमता, सुरक्षितता आणि इष्टतम परिणाम सुनिश्चित होतात.
निष्कर्ष
शेवटी, योग्य ग्राइंडिंग डिस्क निवडणे हे यशस्वी धातूकाम आणि फॅब्रिकेशन परिणाम साध्य करण्यासाठी एक महत्त्वाचा पैलू आहे. निवड विविध घटकांवर अवलंबून असते जसे की काम केले जाणारे साहित्य, इच्छित फिनिश आणि वापरात असलेल्या ग्राइंडरचा प्रकार. मटेरियलची सुसंगतता, अॅब्रेसिव्ह प्रकार, ग्रिटचा आकार, चाकाचा प्रकार, वापर, ग्राइंडरची सुसंगतता, कार्य विशिष्टता, सुरक्षितता, ब्रँड गुणवत्ता आणि किंमत विचारात घेऊन, ऑपरेटर त्यांच्या ग्राइंडिंग प्रक्रियेत कार्यक्षमता आणि सुरक्षितता वाढविण्यासाठी माहितीपूर्ण निर्णय घेऊ शकतात.
ग्राइंडर आणि डिस्क सुसंगततेसाठी सुरक्षा मार्गदर्शक तत्त्वांचे पालन करणे, योग्य वैयक्तिक संरक्षक उपकरणे घालणे आणि उत्पादकांच्या शिफारशींचे पालन करणे आवश्यक आहे. जड साठा काढणे, पृष्ठभाग पूर्ण करणे किंवा कटिंग अनुप्रयोगांसाठी असो, योग्य ग्राइंडिंग डिस्क कामाच्या गुणवत्तेवर आणि कार्यक्षमतेवर लक्षणीय परिणाम करू शकते.
याव्यतिरिक्त, झीज आणि फाटण्यासाठी वेळोवेळी तपासणी, अतिउष्णता आणि कंपन यासारख्या समस्यांचे निराकरण करणे आणि लोडिंग समस्या समजून घेणे यामुळे ग्राइंडिंग डिस्कचे आयुष्य वाढण्यास आणि सातत्यपूर्ण कामगिरी सुनिश्चित करण्यास हातभार लागतो.
थोडक्यात, ग्राइंडिंग डिस्क्स निवडण्यासाठी, वापरण्यासाठी आणि देखभाल करण्यासाठी एक सुज्ञ आणि पद्धतशीर दृष्टिकोन हा इष्टतम परिणाम साध्य करण्यासाठी, उत्पादकता वाढवण्यासाठी आणि सुरक्षित कामाचे वातावरण सुनिश्चित करण्यासाठी महत्त्वाचा आहे.
पोस्ट वेळ: जानेवारी-१२-२०२४